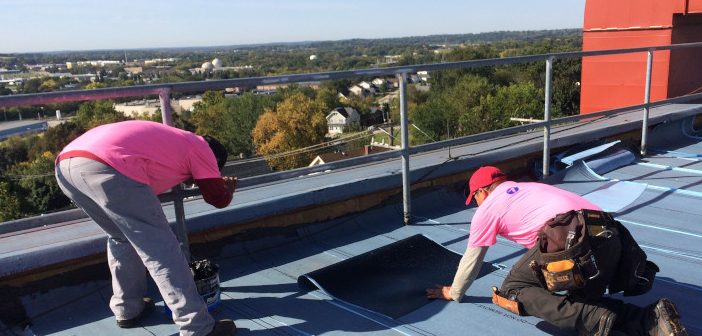
The Need for Speed: Self-Adhered Versus TPO, Single-Ply Roofing
The Need for Speed: Self-Adhered Versus TPO, Single-Ply Roofing
The Need for Speed: Self-Adhered Versus TPO, Single-Ply Roofing
The Need for Speed: Self-Adhered Versus TPO, Single-Ply Roofing
The Need for Speed: Self-Adhered Versus TPO, Single-Ply Roofing
Commercial roofing (i.e. low-slope) jobs come with a lot of variables. Many projects are large in scope, utilize any variety of bituminous application methods, and require tools ranging from kettles of hot asphalt to blow torches. A lot can happen in terms of efficiency and safety that either moves projects along or delays them for weeks at time. Commercial projects also often come with built-in penalties for construction delays that impact a business’ revenue.
For all the reasons above, commercial contractors are always looking for ways to speed projects along without sacrificing safety or quality. While single-ply roof coverings like TPO (thermoplastic polyolefin) have become a common standard for low-slope applications, newer, self-adhered solutions have emerged as an alternative to roof coverings that require torch-applied or hot-mopped asphalt. These self-adhered base and cap sheet products can be rolled out and applied like a powerful sticker to most roof surfaces, but when time is money, do self-adhered products really save the contractor time?
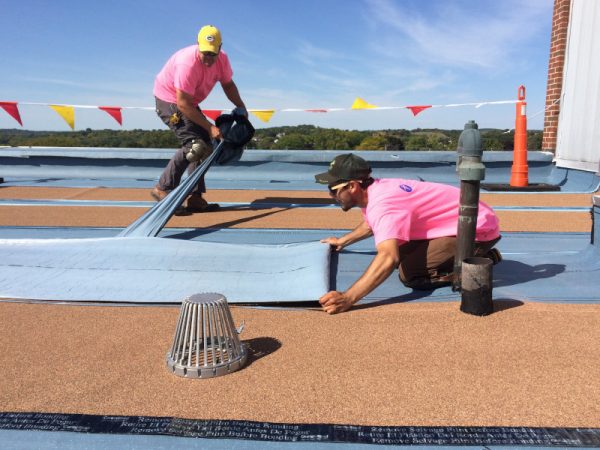
Weighing the Pros and Cons of Self-Adhered and TPO Roofing
TPO single-ply roofing systems have been on the market for more than half a century, so most commercial roofers are familiar with how TPO installs and performs. TPO systems are typically durable; effective in resisting bacteria, debris, algae, as well as ultraviolet (UV) exposure; and relatively low in cost.
Self-adhered modified bitumen roof systems come with many of the same qualities, however, with several advantages. Self-adhered roof systems are installed in two or three layers, reducing the risk of leaks compared to a single-layer installation. Manufacturers have yet to resolve cracking, erosion, and other performance issues that can occur in TPO single-ply roofing membranes after installation.
TPO single-ply roof systems range between 1 and 2 mm (40 and 80 mils) in thickness, while most self-adhered roof systems range from 5 to 10 mm (180 to 380 mils), making self-adhered systems less susceptible to puncture from foot traffic, dropped tools and minor installer errors.
Judging Speed
To answer this question of speed definitively, CertainTeed commissioned a labor study to help commercial roofing contractors improve labor efficiencies and determine which low slope roofing methods were the fastest. To do this, a third-party consulting firm observed the installation of 45 different low-slope roofs with six different roof covers in 18 different configurations across various regions of the U.S. over a five-year span.
Like commercial roofing itself, the study took into account many variables, including project size, climate, installation methods, flashing details and installer errors. While there are no “one-size-fits-all” solutions in the commercial roofing market, third-party data concludes several important details about the speed of self-adhered and TPO applications:
- In a controlled setting, data shows the fastest installed roof covering is a two-ply bituminous system with a mechanically-attached base sheet and a self-adhered cap sheet; the slowest installed system is a bituminous system with both the base sheet and cap sheet installed with hot asphalt.
- On average, a self-adhered roof cover requires 54.2 labor minutes per square while a mopped cover requires 156.5 labor minutes per square – a difference of 102.4 labor minutes per square (2.89 times) or $38,390.63 in estimated project labor costs.
- A bituminous roof cover consisting of a mechanically attached base and a self-adhered cap has a faster installation time than the same base sheet covered with either a torch-applied or hot-mopped cap sheet or a single layer of TPO.
- Flashing details (particularly base flashings and curbs) account for a larger percentage of labor on single-ply projects in comparison to multi-layer bituminous projects.
Conclusions
Under controlled conditions, a two-ply bituminous assembly with a mechanically-attached base and a self-adhered cap is the most labor efficient roof covering. Roof projects, however, are not always applied under ideal conditions. A roof covering alone doesn’t define a project’s labor efficiency or completion time. An individual contractor’s field experience with one or more roof coverings can be a factor. Projects staged with easy material access for installers typically result in faster installations.
Self-adhered roof coverings, however, give contractors additional options when speed, available labor, and client comfort are all factors. Traditional bituminous low-slope roofing installation methods utilizing mopped asphalt or torch welding come with application constraints and safety considerations. These can increase time spent on a jobsite and create challenges for workers, resulting in higher contractor insurance costs. Traditional installation methods can also generate irritating fumes – something to take into account when installing roof coverings on offices, restaurants, schools, hospitals, hotels, care facilities, and multifamily structures, where client comfort is paramount.
While traditional bituminous low-slope roofing installation methods can offer durable protection, commercial roofing contractors facing labor shortages and workflow uncertainty need to be creative in moving efficiently from one project to the next. Self-adhered modified bitumen (mod-bit) systems offer roofing contractors a clean and quick alternative to those installed by traditional methods. When installed properly, self-adhered systems can deliver the protection of those applied with hot asphalt or cold adhesive for a fraction of the workforce training, labor, or time—all without the mess, fumes, hassle, or additional safety risks.